OUR SERVICES
Lower your operating costs while increasing capacity with unprecedented energy efficiency, emissions reductions and fuel savings all in one solution. We engineer, manufacture and integrate custom ConDex Condensing Economizer Systems that allow you to put waste energy back to work.
OUR CLIENTS
- Pulp and Paper processing and
manufacturing enterprises
Kruger Packaging - Montreal, QC
Waste heat from 3 boilers used to heat 2 separate water streams. 36 GPM of boiler make-up water is heated from 70oF to 176oF in the first coil, and 380 GPM of process water is heated from 70oF to 122oF in the second coil. Total heat recovery is 12,020,000 BTU/hr on average.
- Annual average fuel cost savings: $574,400.00
- Annual CO2 emission reductions: 6,588 Tons
- Annual NOx emission reductions: 4.33 Tons
- 6,000,000 gallons/year water recovered
- Payback: Less than 1 year – Installed
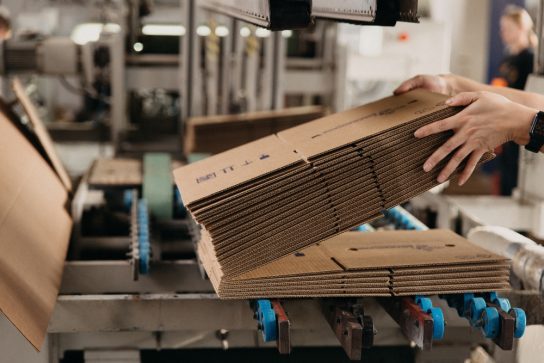
Essity (SCA) - Prudhoe, UK
33 GPM of boiler make-up water heated from 59oF to 194oF using waste heat from 2 boilers. Average heat recovery is 2,260,700 BTU/hr.
- Annual average fuel cost savings: $126,975.00
- Annual CO2 emission reductions: 1,352 Tons
- Annual NOx emission reductions: 0.88 Tons
- 1,140,000 gallons/year water recovered
- Payback: 2 years, 5 months – Installed
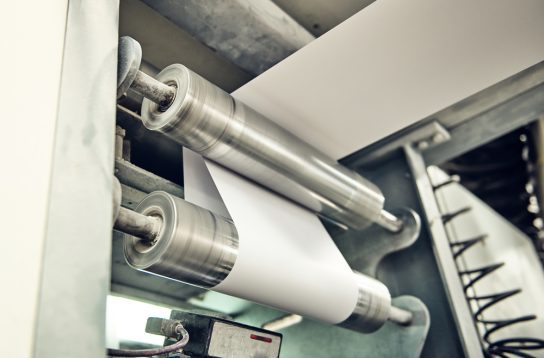
Graphic Packaging - Battle Creek, MI
Waste heat from boiler exhaust used to heat 2 separate water streams. 50 GPM of boiler make-up water heated from 50°F to 190°F in first coil, and 120 GPM of process water heated from 80°F to 160°F in the second coil. Average total heat recovery is 8,390,000 BTU/hr.
- Annual average fuel cost savings: $360,600.00
- Annual CO2 emission reductions: 5,107 Tons
- Annual NOx emission reductions: 3.37 Tons
- 1,368,600 gallons/year water recovered
- Payback: 1 year – Installed
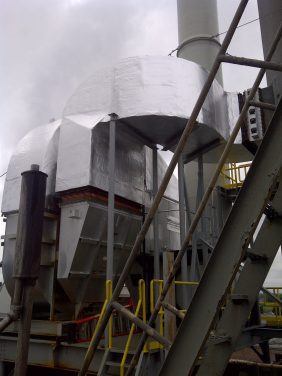
Graphic Packaging - Kalamazoo, MI
Waste heat from boiler exhaust used to heat 2 separate water streams. 250 GPM of boiler feedwater heated from 220°F to 245°F in first coil, and 80 GPM of boiler make-up water heated from 60°F to 190°F in the second coil. Average total heat recovery is 8,470,000 BTU/hr.
- Annual average fuel cost savings: $488,270.00
- Annual CO2 emission reductions: 5,086 Tons
- Annual NOx emission reductions: 3.32 Tons
- 562,400 gallons/year water recovered
- Payback: Less than 1 year – Installed
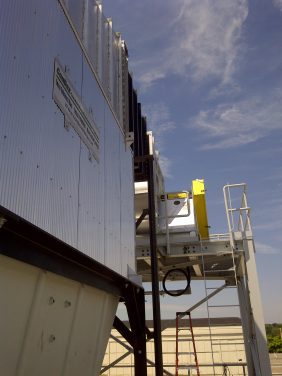